隨著精密加工深入現(xiàn)代工業(yè)制造越來(lái)越多,去毛刺技術(shù)作為工序融入到精密加工中,保證了工件高度穩(wěn)定,防止加工后發(fā)生變形,便于后續(xù)的工藝制程。

毛刺,在金屬制品加工過(guò)程中是無(wú)處不在的“壞小子”,無(wú)論是沖孔、激光切割還是等離子切割,加工工序都會(huì)在工件外表構(gòu)成尖利的毛刺,特別是等離子切割時(shí),熔渣(氧化物和金屬殘留物的混合物)會(huì)頑固沉積在零件邊緣。外表若存在毛刺會(huì)添加人員受傷的危險(xiǎn),危及產(chǎn)品質(zhì)量、影響設(shè)備運(yùn)用乃至縮短設(shè)備的運(yùn)用壽命。比如液壓閥體和氣動(dòng)零件上的毛刺和掉落的金屬粉末,一旦進(jìn)入液壓或風(fēng)動(dòng)系統(tǒng)中將會(huì)發(fā)生嚴(yán)重的紊流或非層流,導(dǎo)致過(guò)濾器或管道阻塞。據(jù)統(tǒng)計(jì),在精密零件加工中,去毛刺的成本約占10%~25%,若精密零件上有深孔和切槽,將使去毛刺成本大大增加。
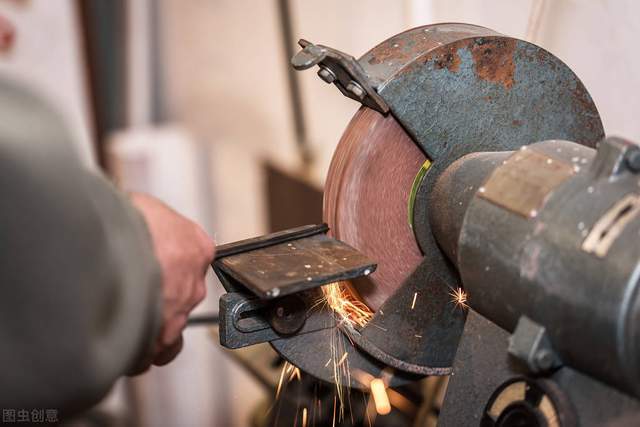
去毛刺技術(shù)為不同制品的精密加工而生,適用于航天航空、汽車(chē)機(jī)車(chē)、半導(dǎo)體、儀器儀表、工程機(jī)械、軍工、高分子材料等高精度要求的元件除毛刺,大幅進(jìn)步出產(chǎn)功率,降低不良品流入市場(chǎng)的概率,降低人工受傷的危險(xiǎn),提升企業(yè)產(chǎn)品出產(chǎn)質(zhì)量。常用的去毛刺的辦法有,電解去毛刺、磨粒流去毛刺、磁力研磨去毛刺、熱能去毛刺、強(qiáng)力超聲波去毛刺、高壓水噴射去毛刺、液氮冷凍去毛刺等,常結(jié)合自動(dòng)化系統(tǒng)操作。針對(duì)不同材質(zhì)工件的外表除毛刺處理,運(yùn)用場(chǎng)景、辦法、溶劑/磨料不盡相同。
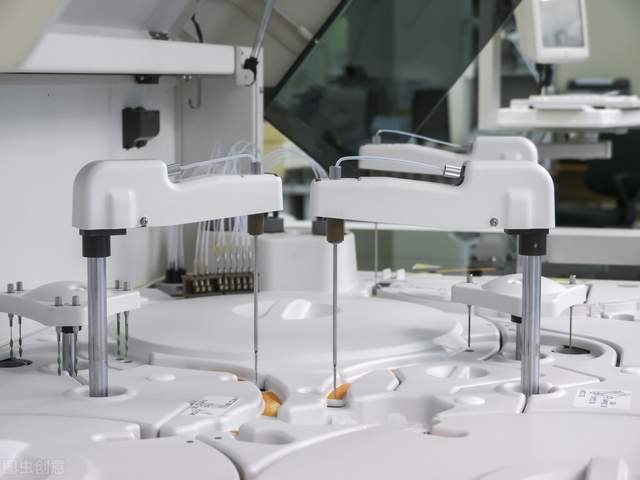
磁力研磨去毛刺,是在磁力去毛刺機(jī)(磁力拋光機(jī))由高速旋轉(zhuǎn)的磁場(chǎng)引導(dǎo)容器內(nèi)的磁針,在清水和拋光液的介質(zhì)中高頻碰擊工件抵達(dá)去毛刺的效果。其原理是磨料在磁場(chǎng)力的效果下沿磁力線方向規(guī)整排列,構(gòu)成一支且柔且剛的磁研磨刷,工件與磨料在磁場(chǎng)中旋轉(zhuǎn)井作軸向振動(dòng)時(shí)發(fā)生相對(duì)運(yùn)動(dòng),磨料刷就對(duì)工件外表進(jìn)行研磨加工。
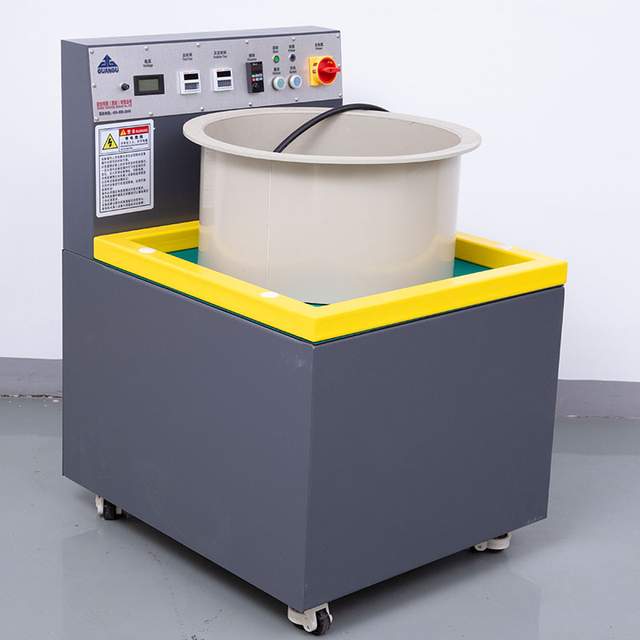
磁力研磨去毛刺辦法有下幾方面優(yōu)點(diǎn):在去除毛刺的同時(shí)對(duì)工件外表進(jìn)行精加工,與磨削加工相比,磁力研磨加工后工件外表光潔度可提高一級(jí)左右;適用于各種精密零件的去毛刺和拋光,可達(dá)鏟除污垢,去除毛刺,進(jìn)步產(chǎn)品外表光亮度;由磁性磨料所構(gòu)成的“拋光刷”能均勻地抵達(dá)雜亂形狀的外表上,因此可一起對(duì)工件的內(nèi)外外表進(jìn)行研磨,針對(duì)小五金件,小飾品等死角,內(nèi)孔處理效果極佳。磁性磨料可重復(fù)運(yùn)用,不需要運(yùn)用水和油進(jìn)行冷卻;磁力去毛刺機(jī)其耗材為拋光液和鋼針,再加適量自來(lái)水來(lái)批量拋光去除工件毛刺即可,對(duì)環(huán)境無(wú)任何污染。